Fließbandarbeit in Leipzig Fließbandarbeit in Leipzig: Im 76-Sekunden-Takt zum neuen BMW
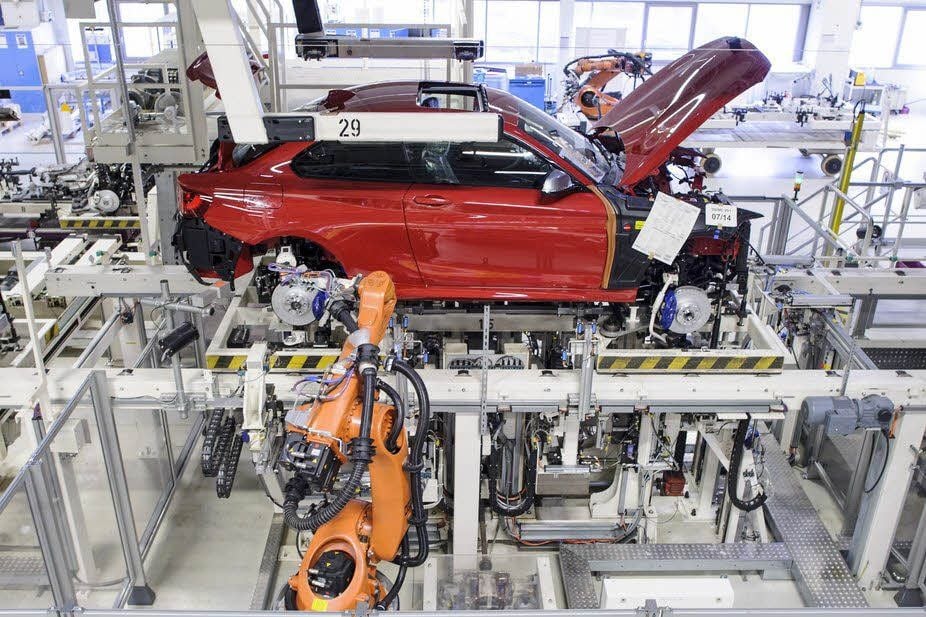
Leipzig/MZ - 76 Sekunden. So lange dauert im BMW-Werk Leipzig ein Takt. Zwei Monteure setzen sich im Schneidersitz in die Karosserie des kleinen Geländewagens X1. Sie verlegen einen sogenannten Kabelbaum. Über diese Leitungen werden später unter anderem Radio und Decken-Leuchte mit Strom versorgt. Jeder Handgriff sitzt, jeder Handgriff wurde schon tausende Male so vollführt. Während der Arbeit läuft das Fließband weiter. Spätestens nach 76 Sekunden muss der Montageschritt erledigt sein. So geht es weiter: Sitze, Fußböden, Seitenspiegel oder Blinker werden in insgesamt 250 bis 300 Takten - je nach Modell - montiert, bis das Auto fertig ist. Bei BMW in Leipzig werden so 740 Fahrzeuge am Tag produziert.
Detroit ist die Wiege
Alle großen Automobil-Produktionen funktionieren vom Prinzip noch heute so, wie sie Henry Ford vor 100 Jahren erstmals einführte. Am 14. Januar 1914 startete der US-Unternehmer das erste mechanisch betriebene Fließband im Ford-Werk Highland Park in Detroit (USA). Anstatt das Fahrzeug handwerklich in einer Manufaktur zusammen zu bauen, wurde eine Massenproduktion errichtet. Dazu wurde der Prozess in etwa 80 Schritte aufgeteilt. Jeder Arbeiter vollführte nur noch bestimmte Arbeitsschritte. Die reine Montagezeit für das Ford T-Modell sank dadurch von über zwölf Stunden auf eineinhalb. Nach der Umstellung konnte Ford das Fahrzeug für 350 Dollar statt 850 Dollar verkaufen. Das Auto wurde damit für breite Schichten der Bevölkerung erschwinglich. Eine Revolution im Automobilbau.
Auch heute setzt jede effiziente Autoproduktion auf eine hohe Standardisierung von Teilen und Abläufen. „Allerdings sind die Produkte sehr viel individueller“, erklärt Markus Grüneisl. Er ist Leiter der Karosserie-Montage bei BMW in Leipzig. Zu Henry Fords Zeiten galt: „Der Kunde kann jedes Auto haben - solange es schwarz ist.“ Heute gleicht kein BMW dem anderen. Die Käufer haben die Auswahl zwischen hunderten Extras. Dies spiegelt sich auch in der Herstellung. In Leipzig laufen über ein Montage-Band derzeit die Modelle X1, 1er BMW und 2er BMW in beliebiger Reinfolge. „Bestellt jemand eine große Stereoanlage für sein Fahrzeug, müssen vielleicht zehn Stecker dafür installiert werden“, erklärt Grüneisl. Ansonsten seien es nur sechs. Große Monitore zeigen den Bandarbeitern an, welche Teile eingebaut werden müssen.
Die Arbeit erfordert hohe Konzentration. Ein Fahrzeug besteht aus etwa 20 000 Teilen, aus etwa 5 000 vorgefertigten Modulen fertigen die BMW-Mitarbeiter in Leipzig das Auto. Funktioniert der Einbau eines Teils am Band nicht oder wird die Taktzeit überschritten, zieht der Monteur die Prozessleine. Ein Vorarbeiter eilt heran und hilft. „Wir versuchen, den Stress für die Mitarbeiter möglichst gering zu halten“ erklärt Grüneisl.
Henry Ford liefen viele Fließbandarbeiter noch davon. Trotz kräftiger Lohnerhöhung und einer Arbeitszeitverkürzung auf acht Stunden am Tag kündigten Bandarbeiter, um dem Arbeitsdruck und der Monotonie am Arbeitsplatz zu entkommen. Volvo wollte daher Anfang der 70er Jahre ein neues Modell einführen. Volvo-Chef Pehr Gustaf Gyllenhammar soll gesagt haben: „Henry Ford hat das Fließband eingeführt. Volvo schafft es wieder ab.“ Der schwedische Autobauer setzte vor allem auf Gruppenarbeit, die die Hetze am Band ablösen sollte. Doch das System war bei weitem nicht so effizient und setzte sich am Ende nicht durch. Ironie: Volvo wurde später von Ford übernommen und gehört nun Chinesen. Die heutigen Automobilwerke sind allerdings ein Mix aus Ford und Volvo.
Nach Worten von Grüneisl wird in Leipzig jeder Bandarbeiter für sechs bis sieben Takte geschult, an jedem arbeiten mindestens zwei Monteure. „Während einer Schicht wechselt jeder Mitarbeiter alle zwei Stunden die Station“, sagt der Leiter. Es sei nicht nur wichtig, Monotonie und damit eine abnehmende Motivation bei der Arbeit zu verhindern. „Vor allem wollen wir eine einseitige körperliche Belastung vermeiden“, sagt Grüneisl.
Das Band, das ist ein weicher Holzfußboden, auf dem die Fahrzeuge angebracht sind. Darauf stehen Tische, die der Mitarbeiter in der Höhe justieren kann. „Jeder Monteur soll seinen Platz möglichst so gestalten, dass er angenehm für ihn ist“, sagt Grüneisl. Unterstützung sucht BMW auch bei den Sportwissenschaftlern der Universität Leipzig, die optimale Körperbewegungen erforschen. Acht Stunden täglich Jahr für Jahr am Band zu arbeiten, so Grüneisl, sei eine hohe Belastung, wenn sie nur einseitig erfolgt.
Der Roboter hält Einzug
Doch nicht nur direkt am Arbeitsplatz wird vorgesorgt: Im werkseigenen Fitnessstudio kann sich jeder Mitarbeiter Ausgleichsübungen für seine Arbeit erstellen lassen. Selbst in den Montage-Hallen gibt es Räume, in denen sich Mitarbeiter in Pausen auf Matten und Gummibällen fit halten können.
Das Arbeitsumfeld möglichst gesundheitsschonend zu gestalten, lohnt sich für BMW. Nach Worten von Werkssprecher Jochen Müller liegt die sogenannte Direktläuferquote bei einem Spitzenwert von 93 Prozent. Das heißt, nur sieben Prozent der produzierten Fahrzeuge müssen vor der Auslieferung - mitunter aufwendig - noch nachbearbeitet werden. 2013 wurde das Werk als „Fabrik des Jahres“ in Europa ausgezeichnet.
Doch irgendwann ist jede Optimierung ausgereizt. Daher kündigt sich im Automobilbau derzeit vielleicht die nächste Revolution an. Die Herstellung der Stahl-Karossen übernehmen bereits Maschinen. Die Automatisierung liegt hier bereits bei 98 Prozent. Doch nun wollen BMW und andere Autobauer den Roboter auch ohne Gitter und Absperrungen als „Kollegen“ ans Band holen. „Dort, wo sehr hohe Präzision gefragt ist, kann der Roboter unterstützen“, so Müller. Ein Beispiel sei das Einsetzen von Scheiben. Noch müsse allerdings umfangreich getestet werden. Eine Auto-Produktion ohne Menschen ist für Grüneisl aber kaum vorstellbar. „Das schöne an unseren Mitarbeitern ist, dass sie bei kleinen und großen Problemen sofort kreativ tätig werden und sie lösen.“ Dies kann bisher kein noch so schneller und präziser Roboter.
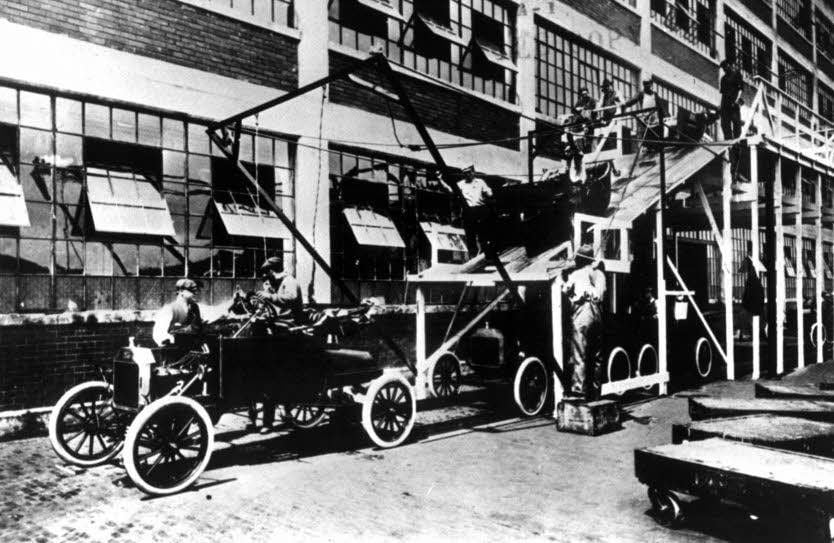
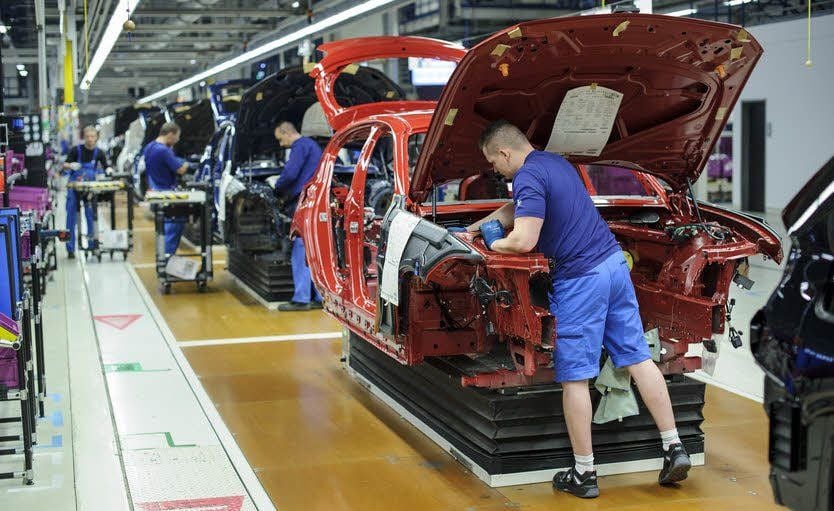